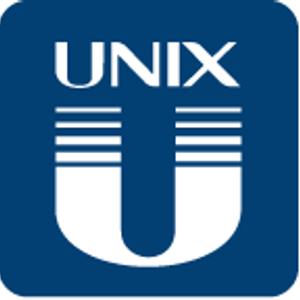
care for tomorrow
- 今後のセミナー
- …
- 今後のセミナー
care for tomorrow
- 今後のセミナー
- …
- 今後のセミナー
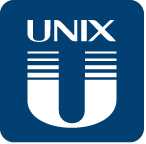
JAPAN UNIX Webinar week 2021
~ 高信頼性はんだ付と自動化 Webinar ~
2021年3月2日(火)~4日(木)
- ~ 高信頼性はんだ付と自動化 Webinar ~2021年3月2日(火)~4日(木)の3日間主催:株式会社ジャパンユニックス協力:IPC Asia Pacific・Robert Bosch GmbH・オムロン株式会社参加費:無料
高信頼性はんだ付と自動化をテーマにおくるジャパンユニックスのWebinar week 2021
1日に2つのセッション(各30分)を計3日間でお届けします。セッション1と2を続けて実施し(計60分)、残りの30分で質疑応答となります。
各日(セッションごとではありません)でのお申込みが必要となりますのでご注意ください。
DAY1 : 3月2日(火) 12:15-13:45 (60分+30分質疑応答)
自動車・車載産業の高信頼性の要求を満たすはんだ付
AUTOMOTIVE&HIGH RELIABILITY DAY
DAY1のテーマは、『オートモーティブ』
自動車・車載産業における国際的なはんだ付に関する品質やボイドの共通認識や標準化動向を、お伝えします。
セッション1 (12:15-12:45)
IPCとオートモーティブ J-STD-001/IPC-A-610GAについて
河野友作, 株式会社ジャパンユニックス
<講演内容>
昨年、世界各国で同時に発行され、大きな注目を集めている、自動車産業の要求を反映したIPCの001/610GAの概要について解説します。
J-STD-001GおよびIPC-A-610Gに対する追加規格「 IPC J-STD-001GA/IPC-A-610GA 車載用途向け追加規格」は、自動化された大量生産ラインという条件を考慮しながら、過酷な環境下のフィールドにおけるミッションクリティカルな車載用電気・電子はんだ付組立品の信頼性を確実にするよう、基準を提供するものである。
セッション2:(12:45-13:15)
SMTはんだ接合のボイド ~車載電子機器における最新動向~
Udo Welzel, Robert Bosch GmbH
<講演内容>
電子アセンブリのはんだ接合部の許容ボイドレベルに関する議論が、車載電子機器を含めたさまざまな業界で大いに盛り上がっている。ドイツ電子技術委員会(DKE)のワーキンググループ内で車載電子機器サプライチェーンのさまざまな利害関係者の間で見出されたコンセンサス概要を示す。※本講演は、音声オリジナル英語、日本語字幕による提供を予定しています。
<プロフィール>
2012年にRobert Bosch GmbHの車載電子機器部門に入社し、現在は、運転支援および自動運転システム用の車載電子制御ユニットのアセンブリおよびインターコネクト技術の統合を担当するシニアエキスパートとしてチームを統率する。標準化活動についての幅広い専門知識を持ち、IPCおよびIECに関わる。IPCでは、プレスフィットおよびA610/J001オートモーティブタスクグループの共同議長を務め、IECでは技術委員会TC91の議長を務める。
DAY1を申し込む
お申込みは日毎になります。セッション単位ではございません。DAY2 : 3月3日(水) 12:15-13:45 (60分+30分質疑応答)
量産導入を実現する最先端レーザーはんだ付とX線CT検査装置
THE LATEST LASER SOLDERING & X Ray INSPECTION MACHINE
DAY2のテーマは、『高信頼性』
高信頼性が要求される量産現場で採用されるレーザーはんだ付の最新事例や工程管理、
"目に見えないはんだ接合部"の品質管理を可能にする高速X線CT自動検査装置をご紹介
セッション1:(12:15-12:45)
レーザーはんだ付 今求められる高信頼性はんだ付
川上信一郎, 株式会社ジャパンユニックス
単点から多点まで、最先端レーザーはんだ付システムで実現する高信頼性と工程管理
<講演内容>
非常に高い繰り返し精度を誇るレーザーはんだ付は、今や高信頼性のはんだ付を要求される車載部品などのアプリケーションなどで非常に多く使用されています。
本セッションでは、高信頼性を実現するためのレーザーはんだ付のポイント、工程管理能力・品質維持に必要な最適化を解説。
最新レーザーの事例として多点や面実装、工程管理のデータ化やトレーサビリティなど、高信頼性のレーザーはんだ付量産体制実現に向けたポイントを解説します
<関連製品はこちら>
セッション2:(12:45-13:15)
電子機器の実装品質課題と高速X線CT検査技術
杉山俊幸様, 村上清様 オムロン株式会社
<講演内容>
量産における外観からのはんだ接合検査の課題は、電気検査では見つからないふぬれ(疑似接触)の検出が非常に重要とされてきた。現在でははんだ形状を3次元で認識する光学検査技術がデファクト化した。しかし、BGAなどの下面電極部品は、はんだ接合部の破壊検査やCT解析機による抜取り確認、2次元のX線による簡易検査に止まっている。
本講演では、高品質が要求される車載等の基板に実際に搭載されている部品電極からはんだ接合品質がどの程度見えているかを概観する。そして量産ラインにて、『自由曲面であるはんだ形状情報』を高速に獲得できる最先端のX線CT検査技術について実績等を交えて紹介する。<プロフィール>
杉山俊幸様
実装品質のコンサルティング業務に従事する技術専門職
- IntPE(JP)/APECエンジニア(Industrial)/技術士(経営工学)/PWBコンサルタント
村上 清様
検査システム事業部 AXIシニアプロダクトマネージャー
<関連製品はこちら>
DAY2を申し込む
お申込みは日毎になります。セッション単位ではございません。DAY 3 : 3月4日(木) 12:15-13:45 (60分+30分質疑応答)
量産ラインにて高信頼性を実現するはんだ付工程
HIGH RELIABLE SOLDRING PROCESS DAY
DAY3のテーマは、『自動化+LIVEデモ』
高信頼性なはんだ付自動化を量産下での成功出来るかどうかは、導入前準備から始まっています。
ここでは導入前後で必要な準備、管理手法、運用管理について解説します。
セッション1:(12:15-12:45)
はんだ付自動化ライン成功のカギ
小島均之, 株式会社ジャパンユニックス
<講演内容>
はんだ付ロボットは導入してからが量産運用のスタートです。本セッションでは、はんだ付の量産ラインの成功に向けた前準備と管理手法、必要な導入プロセス、運用管理について解説します。
弊社の経験豊かなセールスエンジニアが長年の経験で蓄積した、"止めない"はんだ付自動化ノウハウをお伝えします。
<関連製品はこちら>
セッション2:(30分)
導入前テスト・デモのポイントとその目的とは? はんだ付ライブデモ体験
中野和広, 株式会社ジャパンユニックス
今やはんだ付装置の購入決定前に、実際の製品で実験・テスト・デモ(呼び方は様々あります)をすることは常識となりつつあります。昔は、はんだ付が出来るかどうかを知るためのテストではありましたが、今やはんだ付は出来て当然。
シンプルな可不可判定以外にも、量産前テスト、意地悪テストなど様々なテスト目的があります。本セッションでは、様々なテスト内容とその実施目的、必要な体制や準備などを紹介。
本セッションでは、はんだ付ライブデモを通して、はんだ付けプロセスの重要なポイント、テスト・デモの目的を紐解きます。
DAY3を申し込む
お申込みは日毎になります。セッション単位ではございません。
JAPAN UNIX © since 2015